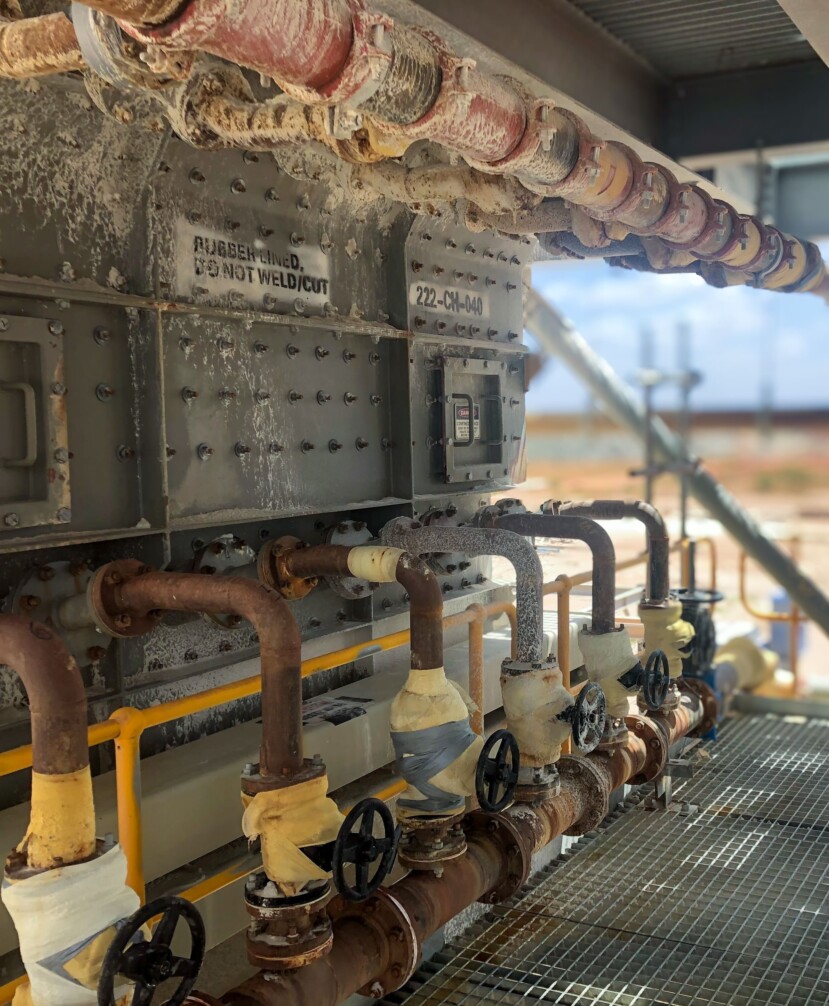
Fast wearing valves take a toll
The team at a lithium mine in WA were plagued by diaphragm valves that were wearing fast from dense slurry water in their FeSi downcomer lines. Their scheduled shutdowns were 20 weeks apart, but the diaphragm valves only lasted 7-8 weeks on average.
Once the valves were worn, the only option was to replace them. This was time-consuming and created lost production costs.
The issue reached boiling point when the team tried to order replacements and found they had snapped up all the available supply in Australia.
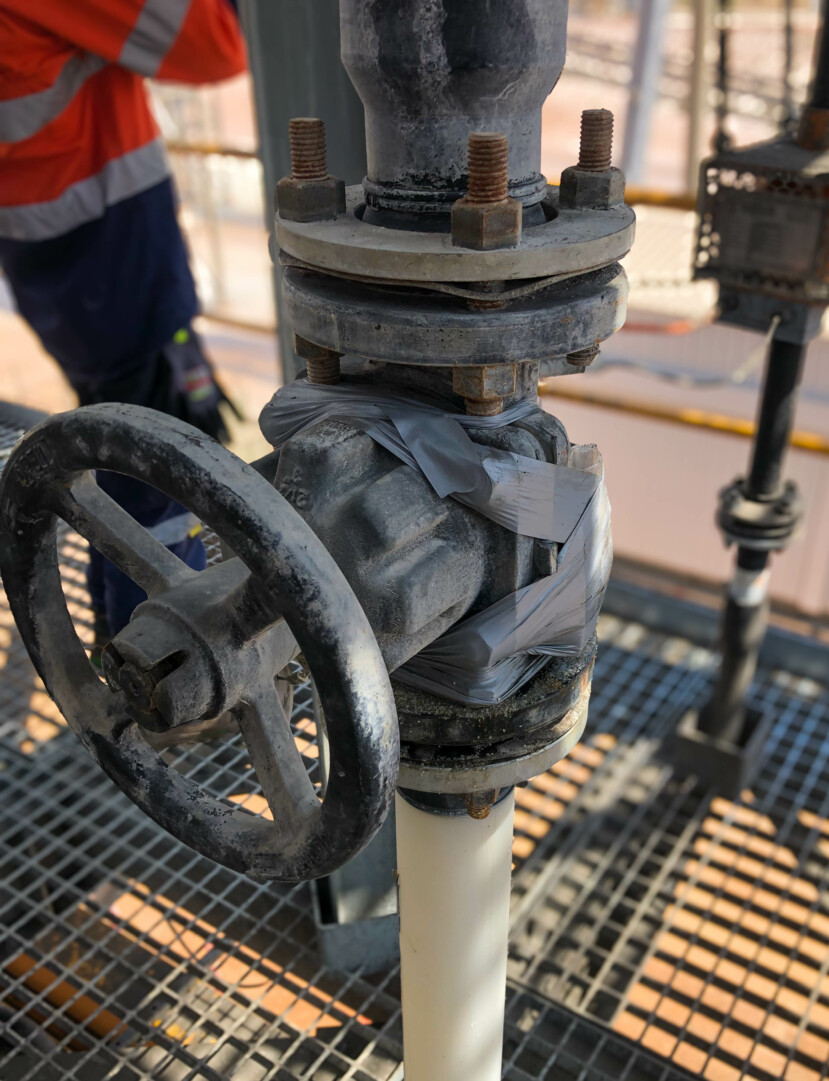
Site visit and analysis
In 2022, the team reached out to us, fed up with their existing setup. They wanted to see if we had any valves that could operate in their harsh slurry conditions.
We went onsite to look at the valves and better understand the problem.
Visual inspection showed that the slurry was wearing the internal diaphragm, causing the failure. Further analysis of the diaphragm showed that it wasn’t suitable for the plant’s chemical conditions.
These manual control valves were also line size or full bore design, with a valve flow coefficient (Cv) that was too high. The required flowrate for the line was low which meant the valves had to be almost closed to achieve the flowrate.
This created high velocity slurry exiting the valve which was damaging the pipework downstream.
The team needed a valve with simple maintenance that could be done onsite. Most importantly, it needed to be able to give the required flow control while handling the high abrasive media.
After reviewing the different options, we recommended the team use heavy duty pinch valves optimised for harsh slurry. The pinch valves have a sleeve that can be replaced onsite with simple tools. The sleeve can also be customised with a specific internal diameter to offer better control.
However, no pinch valves were available that would fit into the tight space already used by the diaphragm valves, and redesigning the pipework to suit the larger pinch valves would be an unnecessary expense.
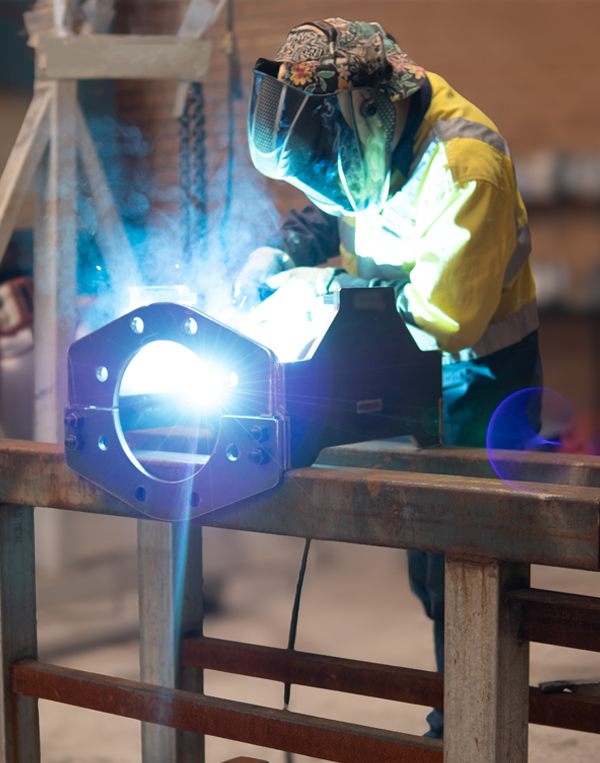
Designing a custom pinch valve and sleeve
To avoid redesigning the piping, our valve team recommended that we design a custom pinch valve with dimensions similar to the existing diaphragm valves. This way, they would slot into place.
We got to work designing a new pinch valve with a modified frame design, which allowed two valves to run parallel without clashing.
If the pinch valve sleeve used the same kind of rubber as the diaphragm valve, it would also wear quickly. So our Brisbane hose manufacturing team created a custom sleeve in our Defender hose factory that uses Grade-A natural rubber and features a reduced port internal sleeve.
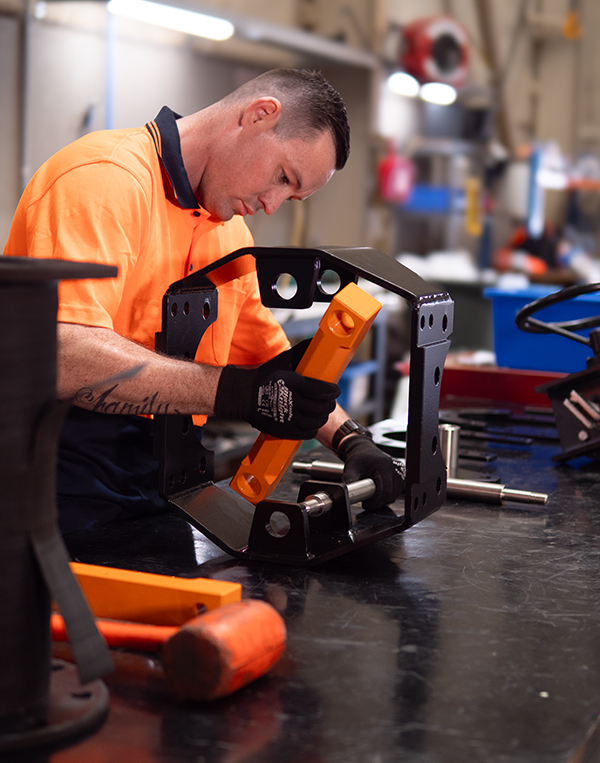
The reduced port internal sleeve means better control over slurry flow as the internal bore is optimised for a specific Cv flow rate. Another benefit of the reduced port sleeve is the valve has a much thicker wear liner, ensuring it will last significantly longer than the diaphragm valves.
The pinch valve’s frame design is split in the middle, which means replacing the sleeve is a simple task that can be done onsite with basic tools. It also means the maintenance team can easily access the valves in the tight area of the plant.
Our Perth valve team designed and manufactured all the valves here in Australia and delivered them to site for replacement.
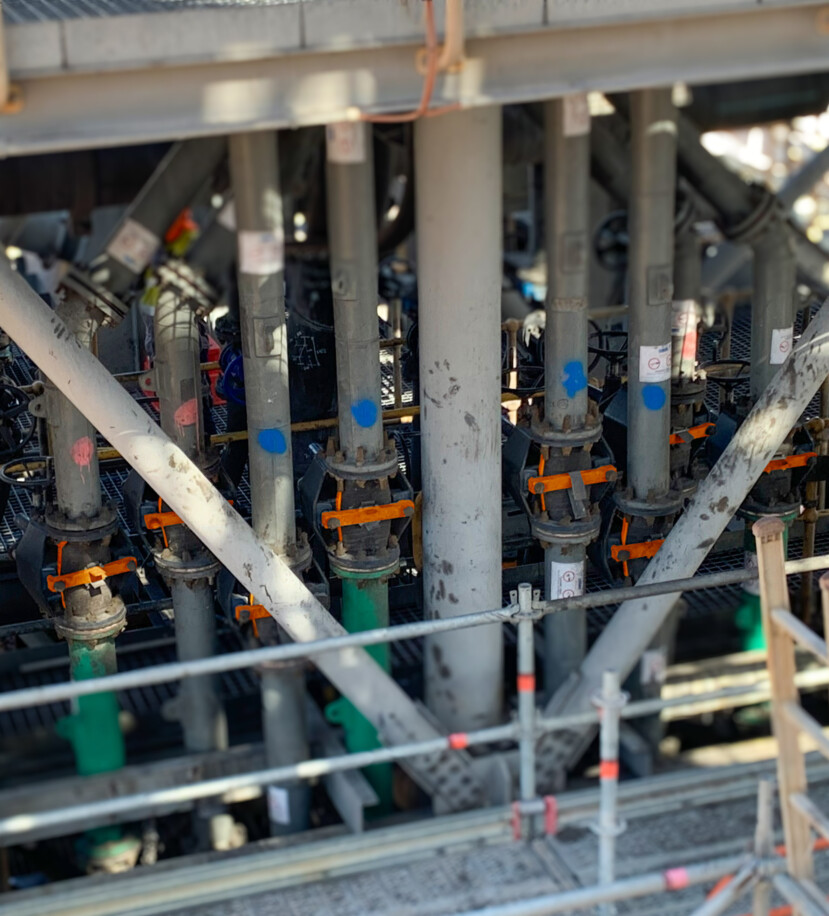
Custom engineered valves make it to shutdown
The team has now replaced all the existing diaphragm valves in their FeSi downcomer lines with the new custom engineered pinch valves. The simple on-site maintenance means they no longer need to order new pinch valves; only the sleeves need to be replaced.
Plus, the sleeves last 12x longer than the diaphragm valves in the harsh slurry, long enough to easily make it to multiple scheduled shutdowns.
The reliability team now has a problem solved. They are more focused on other areas of the plant, and their planners have fewer parts to order, less often.
If you think that a custom-manufactured pinch valve might help you with your site’s problems, get in contact today.
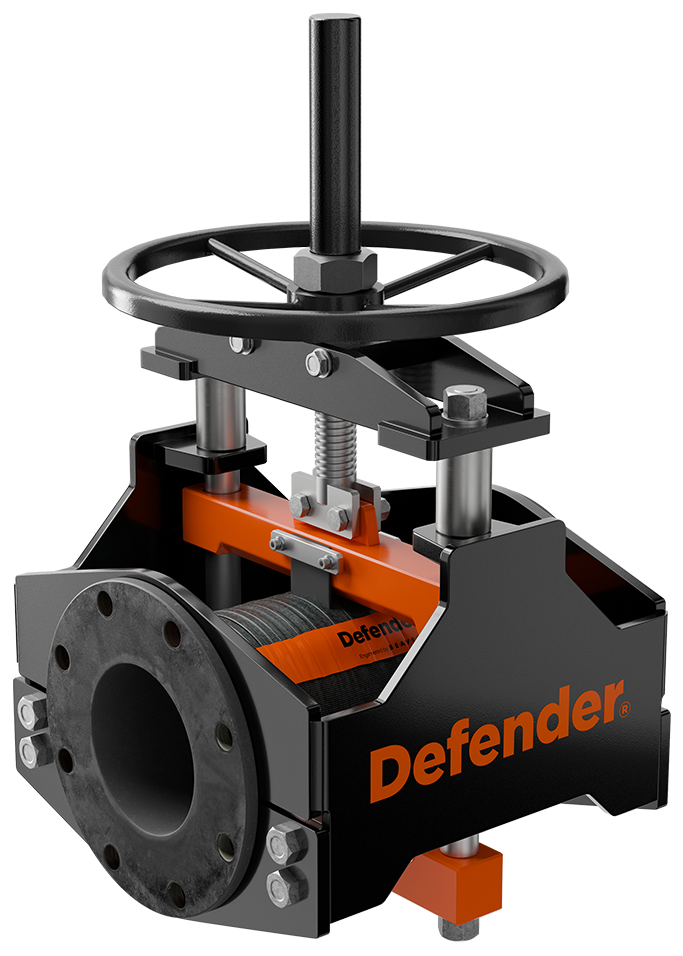