
Pinch valves become a maintenance headache
The team at a gold mine in WA was fed up with fast-wearing pinch valves in their pre-leach thickener underflow line. The valves were set in an awkward position, and maintenance was time-consuming for the team.
Maintaining the valve typically requires replacing the spool, and the valve’s single-body design made accessing the spool for replacement much more difficult than necessary.
The valves were initially part of the new plant design and selected due to their low cost. However, for the maintenance and reliability teams, continuously replacing the sleeve increased downtime and staff costs.
They knew there must be a better way, so they contacted our valve team to see if there was a different valve they could use.
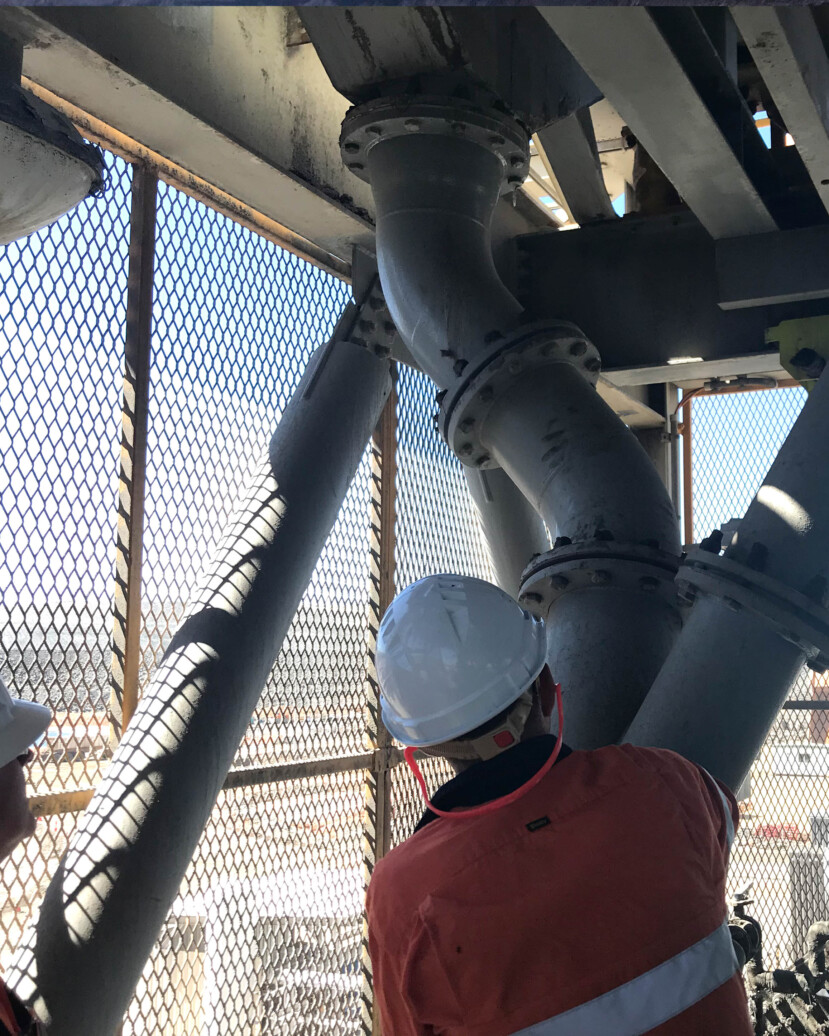
Site visit and analysis
Our valve specialist went to site to better understand their conditions.
The conclusion was that using a pinch valve was the appropriate product, but they needed to upgrade to a heavy duty pinch valve, custom made for their slurry.
Defender pinch valves are custom made to fit into existing pipework by matching the face-to-face and internal diameter of the existing pipework. The valve has a replaceable sleeve that can be maintained onsite with simple tools and the sleeve can also be customised to suit optimal slurry flow.
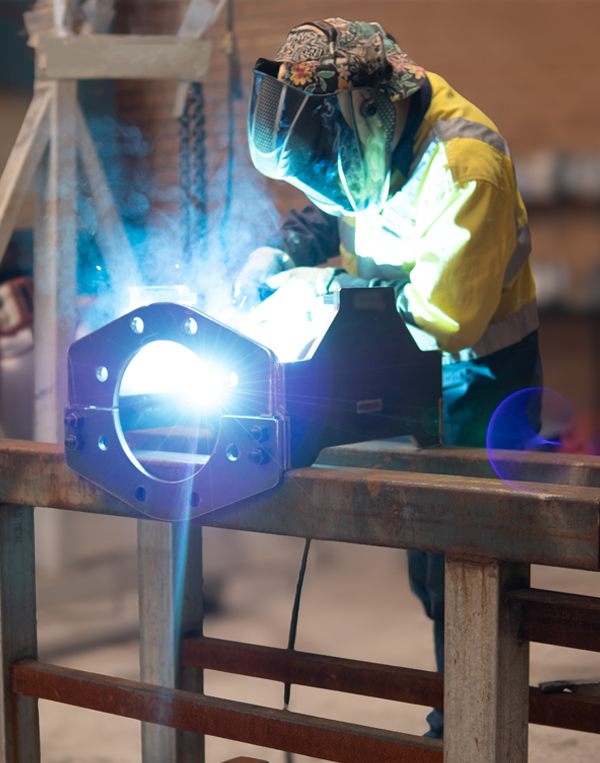
Custom design and replacement
Given the clear application of a pinch valve, our team recommended that we design a custom pinch valve with the same dimensions as their existing pinch valves. This way, they could slot into place.
The other concern was the pinch valve sleeve because using the same kind of rubber as the existing pinch valve would only delay inevitable failure. So, our Brisbane hose manufacturing team created a custom sleeve in our Slurryflex hose factory that uses Grade-A natural rubber and features a reduced port internal sleeve.
The reduced port internal sleeve means the team has much better control over slurry flow, as the internal bore is optimised for a specific KV flow rate. The valve also has a much thicker wear liner, ensuring it will last significantly longer than the old pinch valves.
The upgraded pinch valve’s frame design is split in the middle, which means replacing the sleeve is a simple task that can be done onsite with basic tools, even in tight areas of the plant.
Our Perth valve team designed and manufactured all the valves here in Australia and delivered them to site for replacement.
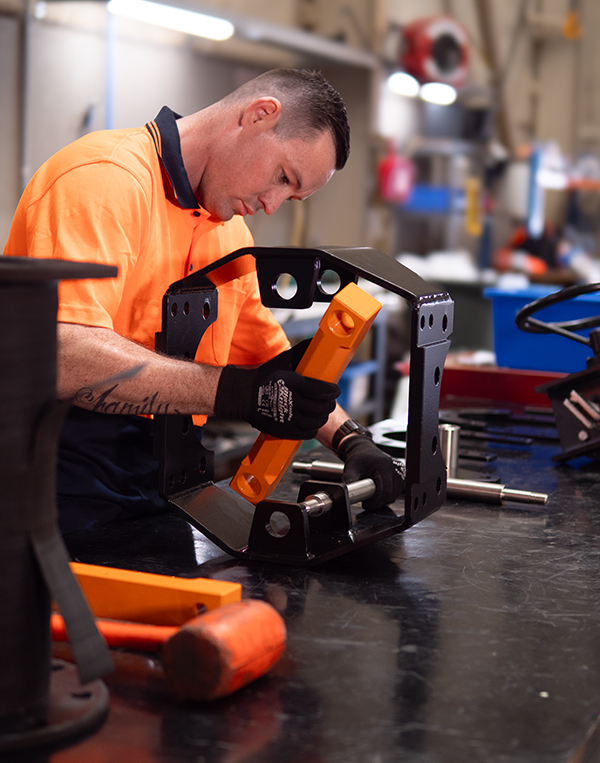
Upgraded pinch valves outperform
The team has now replaced all their conventional pinch valves with their new custom made Defender pinch valves. The Defender valves are heavy duty and made to last in their tough slurry conditions.
Maintenance on the valve is easy: The sleeve is replaced once every 2-3 months, compared to the 7 weeks they used to replace the sleeve in. That’s a 6x longer wear life.
The reliability team now has a problem solved. They are more focused on other areas of the plant, and the maintenance team spends less time maintaining the pinch valves.
If you think a custom-manufactured pinch valve might solve your site’s problems, contact us today.
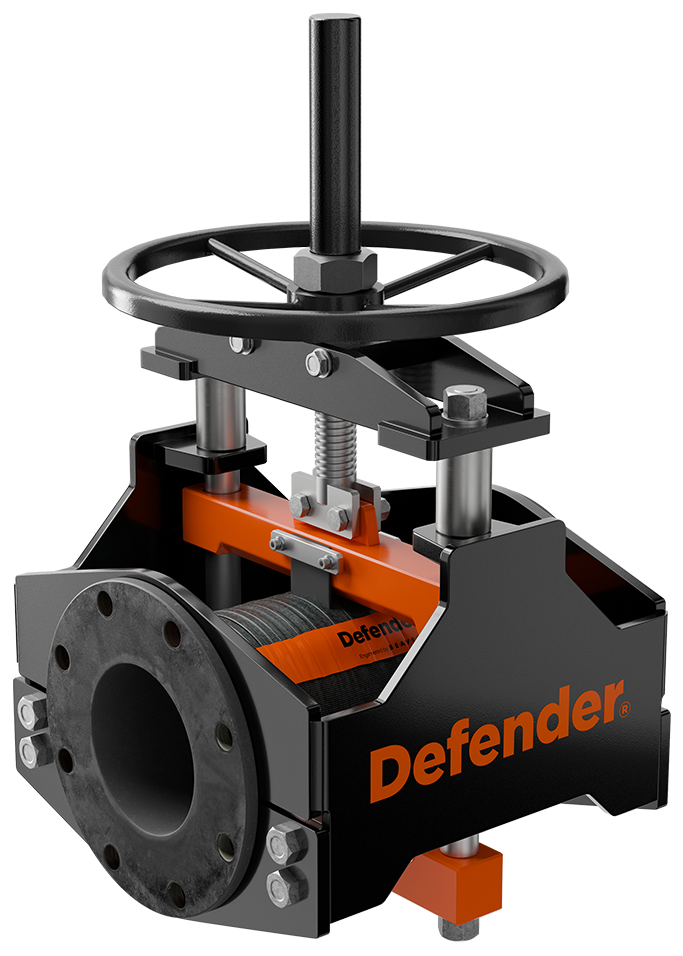