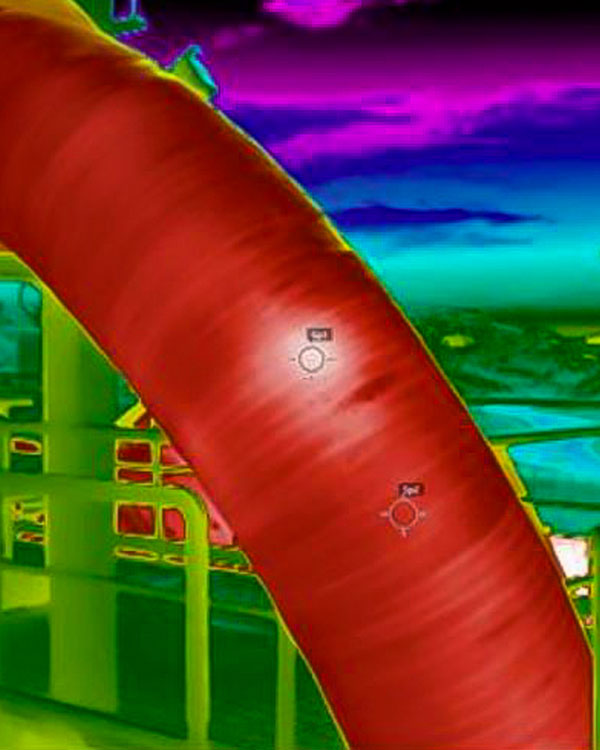
The Challenge
Back in 2019, the reliability foreman contacted us to see how he could reduce downtime on the mill feed line, caused by blown-out pipework.
Over the years, they had trialled numerous types and brands of piping including HDPE, rubber-lined rigid steel, and mining hose. The best-wearing option they had found—standard mining hose—was still only lasting three months.
It was a constant source of frustration for the crew. The downtime to fix worn and leaking pipework was costly. Plus, the time to remove and replace the pipes during scheduled shutdowns slowed down maintenance in other areas of the plant.
The reliability team had thermally scanned all the pipework, revealing a series of wear hot spots. They knew that this was the source of their problems, so began looking for better options.
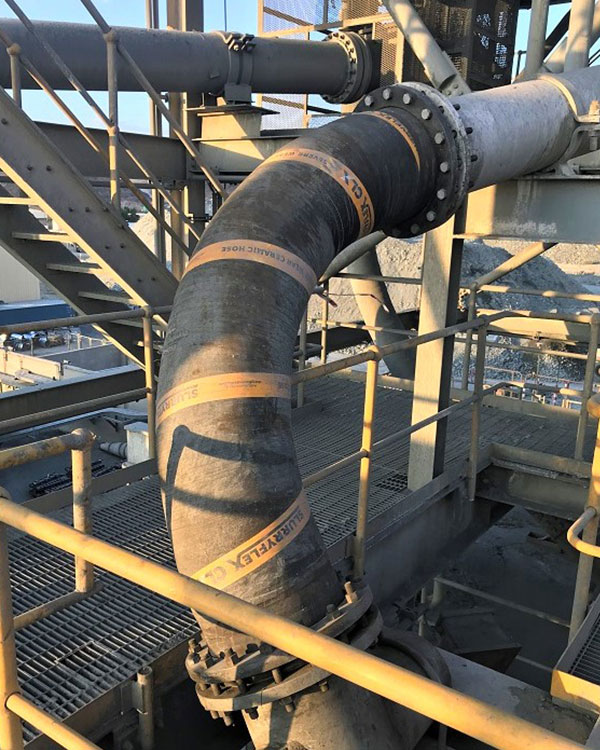
Wear diagnosis
Mill feed lines take a beating. A common problem here is extreme, localised wear on piping bends as high-velocity slurry exits the ball mill. It chips and gouges piping until it leaks and fails.
Mining hose had performed better than rigid pipe in the feed lines previously because it can absorb and dissipate slurry impact throughout the entire carcass of the hose. This reduces localised wear points. However, if the slurry is particularly abrasive, it quickly gouges through hose liner.
After speaking to the foreman and reviewing the information they provided, we suggested they trial ceramic-lined mining hose.
Ceramic-lined mining hose is flexible but adds an extra layer of wear resistance. Alumina ceramic tiles are embedded into the hose liner during the manufacturing process. This makes it more durable by reducing cutting from sharp particles.
The outcome
The foreman ordered a preformed DN400 Slurryflex CLX bend to trial against standard mining hose. By the three-month mark, the mining hose had worn through, while the Slurryflex CLX hose was still going strong.
Since it was first trialled, Slurryflex CLX has consistently lasted more than twice as long as the previous alternatives.
The team has stretched the intervals between planned shuts and reduced the time and cost of replacing the worn feed lines. It’s worked so well that they’ve installed it in other high-wear areas of the plant.
For the reliability foreman and his crew, it’s a big win. No more leaks, no more costly unplanned shutdowns, and more time improving other areas of the plant.
Lifespan 2x longer than regular mining hose
Durability No more bandaging leaks
Custom made Engineered to specification
Maintenance win Longer shutdown intervals