Newcrest’s Cadia Mine – Custom Slurryflex CLX Reducer
The reliability team at Cadia mine have eliminated a long-term maintenance problem by replacing a single slurry pump spool.
Located near Orange in NSW, Cadia is one of Australia’s largest gold mining operations. Slurry in the process plant is turbulent, high velocity and severely abrasive—a recipe for fast wearing pipework.
After many years of experiencing failures with rubber-lined pipe and direct-bond ceramic pipe, they were frustrated and went looking for a better way.
That’s when we offered to help. We realised they needed a way to:
1. Dampen the vibration
We recommended ceramic-lined mining hose to do this. The rubber hose carcass has absorbing properties. It dampens vibration and noise, rather than sending the vibration back to the pedestal. This gentler response increases the wear life of the pump bearings.
2. Handle the rough slurry conditions
We recommended Slurryflex CLX because it has ceramic tiles embedded into the rubber. This makes it more durable against abrasive slurry, meaning less downtime for unscheduled maintenance.
3. Make shutdowns and installation faster and easier
Mining hose is easier to install—the axial elongation properties mean you can bend, stretch or compress it into place, if necessary.
This photo shows the new Slurryflex CLX mining hose installed on site. We custom manufactured it in our Brisbane factory with 360° tiling at DN300 size.
Two years on, the reducer is still going strong. With this small change, the team have fixed a long term maintenance headache and improved throughput.
Client
Year 2021
Location NSW
Commodity Gold
Application Custom mining hose reducer
Outcome 2+ Year Wear Life
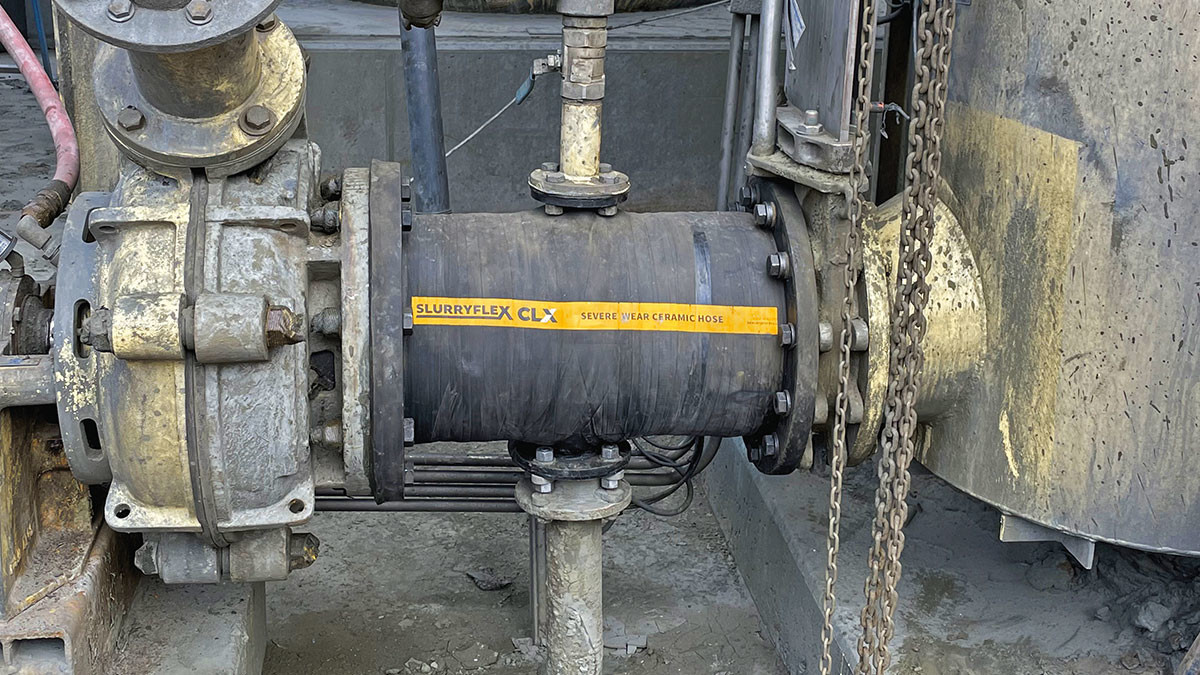
Related projects
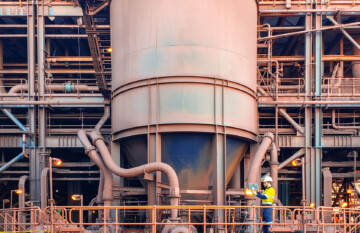
How Roy Hill Solved Costly Unplanned Piping Maintenance for Good
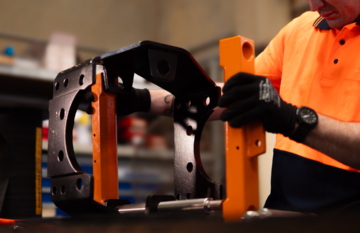
WA Lithium Mine get 12x Longer Wear Life in Slurry Control Valves
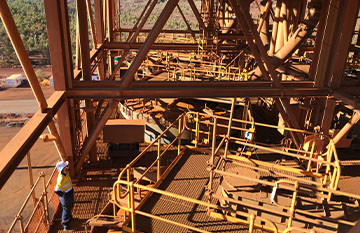
8x Longer Lifespan for Cyclone Overflow Piping at FMG Solomon Mine
We're here to help
Got questions? Need advice? Tap into our experience and get specialist advice from our friendly team.
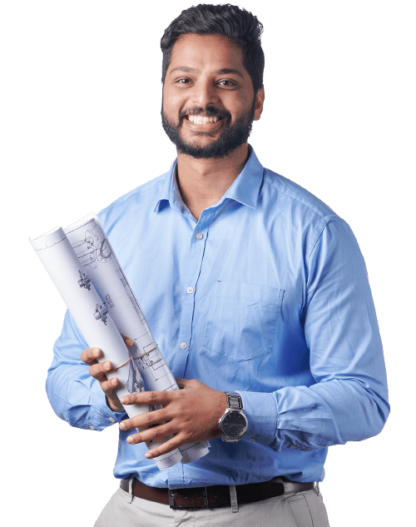

Slurry piping audits
Solve slurry piping maintenance problems for good. No more leaking pipes, no more unplanned shutdowns.