Hydrocyclones are critical pieces of equipment, but frequent piping failures can make them a maintenance nightmare.
When they go down, it can directly impact your plant’s availability and your production targets.
The three high wear areas in hydrocyclones that typically create the most work are:
- Feedline piping
- Cyclone overflow piping
- Cyclone underflow piping
Here’s what goes wrong in each area and how to fix it.
Cyclone Feedline piping
What goes wrong with feedline piping?
In our experience, the most common wear spots on cyclone feedlines are the feedline bends and the pump discharge spool.
The first and second bends cop most of the wear as the slurry exits the pump because the slurry is turbulent and fast moving. When it hits the side of the bend, it creates a localised wear spot that quickly holes out.
The discharge spool – in most cases a short reducer – is also a high wear point. It connects directly to the pump and takes an extreme amount of turbulence and vibration.
How to fix your feedline and slurry pump piping
Redesign feedline bends as long sweeping curves, this will reduce localised impact wear.
To combat the fast wear, you also should use piping that has both high abrasion resistance and impact absorption. A good option is a ceramic lined mining hose.
Mining hose works well on bends because it’s flexible, so it absorbs and dissipates slurry impact. Its flexibility also works well for reducers, absorbing vibration wear from the pumps.
Cyclone overflow piping
What goes wrong with overflow piping?
Cyclone overflow piping carries the finer ore slurry away from the cyclone. The strange thing about overflow slurry is that it’s generally less abrasive but the piping is more prone to wear.
Why is that? Two reasons:
– Tight geometry. The bend radius on overflow piping is usually very tight. Tight bends create localised wear points when slurry hits them at high speed. In most plants the highest wearing point is the outlet flange because the slurry is most turbulent when exiting the cyclone.
– Poor piping selection. HDPE and rubber-lined steel are still used far too often on cyclone overflows. These older lining types are completely unsuitable for overflow piping because they wear quickly in turbulent, abrasive conditions.
How to fix your overflow piping
There’s actually a very simple fix for your cyclone overflows. Use the right type of piping for the job.
If you use a ceramic lined mining hose, you’ll get far better wear life than rigid piping because it withstands particle impact and abrasion wear.
One of our customers switched from HDPE to mining hose for all their overflow piping and got 9x longer wear life. They:
- Addressed the impact absorption and wear problems: Replacing rigid piping with flexible mining hose drastically improved wear .
- Redesigned the bend radius: They redesigned the overflow piping with smoother bends, which reduced localised impact wear.
- Simplified inventory: When they redesigned the bends, they created one and two-piece bends. With only two types of bends, this has made their hydrocyclone maintenance and inventory management simpler.
Cyclone Underflow piping
What goes wrong with underflow piping?
Cyclone underflow piping is typically gravity-fed. Slurry free-falls at speed and then hits the same spot which creates a localised wear point on the bend arcs.
Many sites try to fix this by changing from rubber-lined steel to ceramic-lined steel.
But that doesn’t work.
Steel is rigid and the ceramic is hard, so it has even less impact absorption than rubber lined steel. When the slurry hits the bend, the tiles chip, erode and peel off. After that, it’s only a matter of time before the pipe fails.
How to fix your cyclone underflow piping
In freefall gravity fed lines like cyclone underflows, bends perform better when they can absorb the impact. That’s why mining hose works well in underflows – it can handle impact absorption much better than HDPE or rubber lined steel.
It has worked well for the reliability team at this iron ore mine in Western Australia. Their pre-formed mining hose bends have lasted six times longer than rubber-lined steel.
Improving uptime in your cyclone piping doesn’t have to be complicated
Now you know how to fix the most common wear problems in cyclones. Choose the right piping and it will pay off with improved reliability and uptime.
Many of our customers have made big improvements to their plant uptime and availability by tackling these problem areas. Talk to us if you’d like to find easy ways to do the same in your plant.
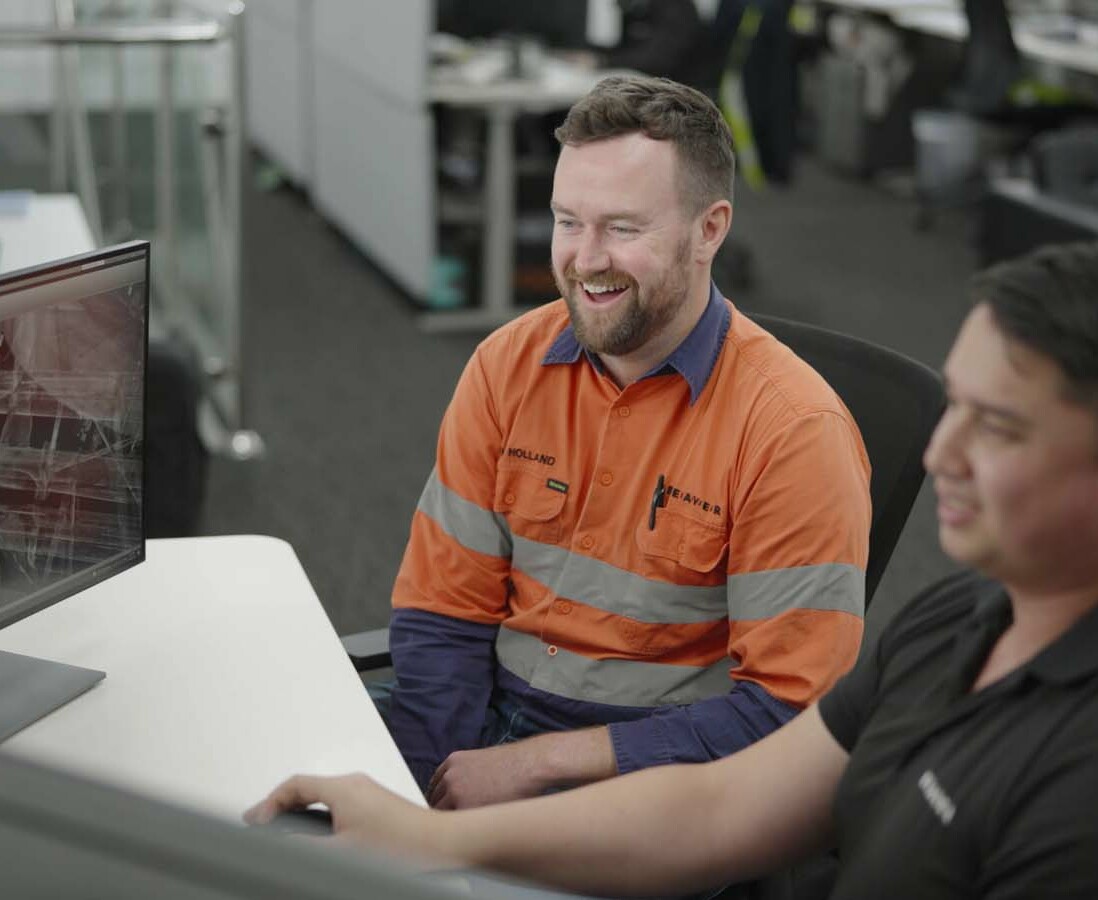
Get practical recommendations for your cyclone piping
Get in touch to setup a call with our piping specialists. We'll give you clear recommendations and advice to help you improve the wear life and reliability of your cyclone piping.
"*" indicates required fields