Gold slurry is tough to work with. It’s abrasive – that’s why your slurry piping and pumps take a beating.
Keeping your gold process plant up and running has another challenge. These plants are built to a budget, so designers typically have to cut corners on the slurry piping. That’s why your team now spends way too much time bandaging and replacing spools.
The good news is it doesn’t have to be that way.
Let’s look at five established gold mines and how they fixed common piping problems in their processing plants.
1. Cyclone overflow redesign: Martabe Gold Mine
At Martabe, HDPE piping on the cyclone overflow was only lasting 2,100 operating hours, or three months of service. It was a lengthy, arduous job to fix and the impact on plant throughput was significant.
Fast wearing bends in cyclone overflows are common in gold plants—we see it all the time. It’s compounded by the fact that HDPE just isn’t suitable for this part of the plant.
The plant reliability engineer realised that simply replacing the same spools over and over wasn’t sustainable.
After reviewing the options, he decided to redesign the piping to create a more sweeping bend to reduce turbulence. He also installed Slurryflex CLX ceramic-lined mining hose to get longer wear life from the ceramic tiles, as well as flexibility to absorb impact and make installation easier.
With better design choices, he now gets more than 17,000 hours of service – an 9x improvement on HDPE spools.
2. Slurry pump piping: Newmont Tanami
At Newmont’s Tanami gold mine, the maintenance team was constantly pulled away from other tasks to fix leaking slurry pump pipework. Vibration from the pump was causing pipe misalignment, frequent leaks, and unscheduled maintenance.
The site was using two rubber-lined spools—a straight spool and a reducer—and a flexible coupling to connect the pump and adjoining pipework.
It’s a common set up around slurry pumps because of how difficult these spools can be to replace. It’s a fiddly and time-consuming job, made easier by using a coupling.
That’s why we recommended they introduce flexibility. They realised that mining hose spools were easier to install. And they handled the shock and vibration better, extending wear life and reducing pump wear at the same time.
The Tanami team replaced the two spools and coupling with a Slurryflex SD Series reducer mining hose. A simple modification that now lasts twice as long and has eliminated unscheduled repairs.
3. Cyclone feed elbows: KCGM Fimiston
The rubber-lined steel spools on KCGM’s cyclone feed were only lasting 3-6 months. Not only were they wearing too quickly, it was out of sync with the plant’s shutdown schedule. For the reliability team, that meant a lot of bandaging and patching to keep things running.
During our site visit, we identified that the tight geometry was causing the accelerated wear. We recommended redesigning the piping geometry with flexible mining hose for more sweeping bends. This reduces turbulence, absorbs vibration, and extends the lifespan of the pipework.
To help the team better predict when the band was wearing, they installed wear monitors. That way they had advance warning of when an elbow was about to fail.
They decided to install Slurryflex ceramic lined mining hose to beef up the wear resistance. Two years later, the mining hoses have lasted five times longer than the previous rubber-lined spools. It has eliminated leaks and unplanned shutdowns and the maintenance team can now easily predict when they can need to replace the bends.
4. Ball mill piping: AngloGold Tropicana
Ball mill piping takes a beating. For the team at AngloGold Ashanti’s Tropicana mine, rubber lined spools in the discharge piping were failing every six months. It was hurting throughput and leading to unplanned shuts to bandage the worn and leaking piping.
Grinding circuits are one of the highest wearing places in a plant for piping. Abrasive slurry discharges at high speed and turbulence is common, along with worn and jagged steel ball chips.
They realised they needed to change from rubber-lined spools to something with better wear performance. Rubber lined steel is the default choice to upgrade from unlined steel or HDPE, but is an old technology and often not the best option.
They decided to trial Abrasiguard polyurethane-lined piping. We recommended it for their milling and grinding areas due to its abrasion, corrosion, and impact resistance.
Their trial paid off and the team now gets more than 4x the wear life from their discharge piping. They can extend the intervals between shutdowns and free up time – and budget – to focus on improvements in other areas of the plant.
5. Gravity fed piping: Northern Star Carosue Dam
For the maintenance super at Northern Star’s Carosue Dam gold mine, impingement box feed line piping was his main problem in the plant.
Only lasting 2.5 weeks before leaks began, the maintenance crew were constantly bandaging the ceramic lined steel spools.
It’s hard to get good wear performance from steel spools on gravity fed lines. In this area of the plant, you need piping that is extremely wear resistant and flexible to handle impact.
They chose ceramic lined mining hose for the elbows. Rubber mining hose absorbs and dissipates impact from the fast slurry when it changes direction on the bends. For the straight spool, they opted for Abrasiguard polyurethane-lined pipe because its wear liner is smooth and durable to withstand the rough sliding ore.
This combination of flexibility and extreme wear resistance outperformed the ceramic lined spools by more than 4 times. The team is now freed up to focus on other maintenance jobs in the plant.
The power of small change
The reliability and maintenance teams at these sites found that making small improvements to their slurry piping systems paid off.
They put an end to piping frustrations that were stopping them from hitting their production targets.
The areas we have outlined in this article are common problems areas on nearly every process plant we visit. If you’re looking for easy maintenance wins, start with these.
You’ll spend less time on the maintenance merry-go-round and have more time to focus on making bigger productivity gains in other areas of your plant.
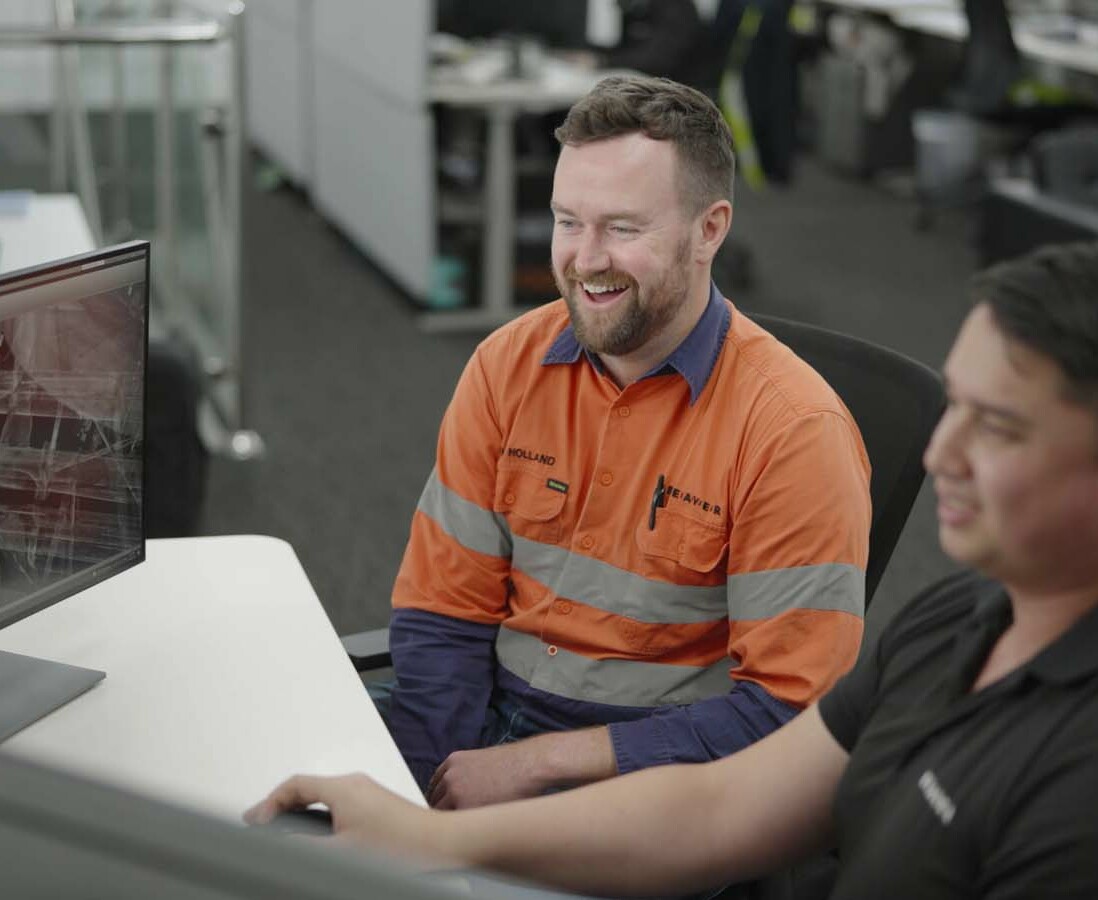
Tired of frequently replacing slurry piping?
Find easy wins for your plant. We’ll share real examples of sites like yours getting longer wear life and better reliability from their slurry piping and how you can achieve the same.
"*" indicates required fields