Your slurry pumps are the heart of your processing plant. If they go down, it can bring production to a complete stop.
One critical part of slurry pump reliability that can be overlooked is the piping.
There are four common problems we see with slurry piping around pumps.
- Excessive pipe wear
- Vibration damaging pumps and other equipment
- Pump piping that’s hard to install
- Leaking couplings and end connections
This guide will help you avoid these problems in your plant. So you won’t have to worry about unexpected failures or fast-wearing pump piping again.
Problem #1: Excessive pipe wear
There are three main wear types around pumps:
Erosive Wear
Erosive wear is when the wear liner is worn down due to turbulent and fast-moving slurry. It can wear through the liner in rubber lined steel and cause the liner to debond and peel away.
It’s most common on the straight spools attached to the pump and is made worse by pump turbulence.
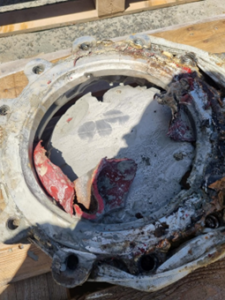
Pictured: Erosive wear lead to the rubber debonding and it got caught upstream
Impact Wear
Impact wear is a type of erosive wear. It happens when slurry hits the side of the bend repeatedly and creates a concentrated wear spot. It’s most common on the first bend in the discharge line.
Rigid piping like rubber lined steel accelerates this type of wear because it has limited shock absorption.
Leading Edge Wear
Leading edge wear happens when the internal diameter (ID) of adjoining pipes is mismatched.
Often this is because different spools are upgraded to different materials, or wear liners.
Slurry will catch on the lip of the smaller ID and wear through the join. This damage creates leaks and adds to slurry turbulence.
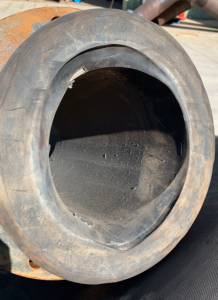
Pictured: Clear signs of leading edge wear
Do this instead:
Here’s how to address each wear type:
Erosive Wear
Pump piping combats erosive wear better if you use a more wear resistant liner, like polyurethane.
Polyurethane lined pipe has better wear resistance than rubber lined steel in turbulent pump slurry.
Also, the polyurethane liner is bonded to the steel substrate during manufacturing so it can’t debond and peel away.
Use polyurethane lined pipe on your straight spools near pumps to avoid erosive wear or your liner debonding.
Impact Wear
To handle impact wear better you need to reduce localised wear points and improve your piping’s impact absorption.
Redesign tight bends close to the pump as long sweeping curves, this will reduce the localised wear points and impact wear.
Mining hose works better for impact absorption because it has more ‘give’. When hard, fast-moving slurry hits the hose wall, particles are deflected, and the impact is absorbed across the entire hose.
If your slurry is severe wearing, you can upgrade from a standard mining hose to a ceramic lined mining hose. Our customer did this upgrade to their slurry pump piping and got six times better wear life, you can read about that here.
Leading Edge Wear
To prevent leading edge wear you need to make sure your ID’s are the same on adjoining pipework.
To do this, use polyurethane lined pipe and mining hose. Both can be customised to match the ID of adjoining pipework.
You can match ID’s with mining hose because we build mining hose from the inside out. It starts with a mandrel the precise size of the bore and we add layers to build out the hose.
Polyurethane lined pipe also lets you control the ID. We make it by spin casting the polyurethane, for millimeter accuracy.
Use mining hose on your bends or reducers and use polyurethane lined pipe on your straights. This will eliminate any leading edge wear.
Problem #2: Vibration damaging pumps and other equipment
Pumps can be noisy and create a lot of vibration. When you use rigid piping it makes the vibration worse.
Rubber lined steel is a common piping choice around pumps, but it can’t absorb pump vibration because it’s rigid. It feeds the vibration back into the pumps, which damages the pumps and adds to the noise.
This vibration feedback speeds up pipe wear and can create pipe misalignment. This causes leaks and premature spool failure.
Do this instead:
To absorb the vibration and noise, use a single mining hose reducer or a rubber expansion joint close to your pumps.
They will absorb the vibration and spread it across the hose length.
This reduces the impact of turbulent slurry exiting the pump, lowers stress on the equipment, and reduces noise.
It also makes installation much quicker, which is our next point.
Problem #3: Pump piping that’s hard to install
Pump piping needs to be quick and easy to install.
If you’re using rigid spools like rubber lined steel, your alignment must be spot on. They can’t be manoeuvered into place if out of tolerance.
Take a look at this example from one of our customers. Their design tolerances didn’t allow for the misalignment between the pump and discharge piping.
Do this instead:
To make your installation faster and accommodate for misalignment, you need to add flexibility to the line.
In the example above, the fix was to replace the rubber lined steel spool attached to the pump with a mining hose.
This makes installation much simpler because the mining hose is flexible. That means if there’s pipe misalignment, you can stretch, compress, and rotate the hose to bolt it onto the pump.
Installation is also faster with mining hose as you eliminate the flexible coupling needed to join two rigid spools. If you get rid of the coupling you’ll avoid leaks too, which is our next problem.
Problem #4: Leaking couplings and end connections
Here is a typical pump piping setup we see often, it has two rigid rubber lined spools and a flexible coupling to join them together.
The flexible coupling is a hotspot for fast wear and leaking slurry.
Coupling misalignment will allow slurry to leak out, which creates a safety hazard and messy clean up job.
Pump vibration will accentuate this type of misalignment and speed up the time to failure.
“The most common slurry pump piping setup we see is two rigid spools, usually rubber lined steel, and a flexible coupling.
It’s done at the design stage to accommodate for installation tolerances, however it’s often not enough flexibility.
This can all be avoided by using mining hose instead. It has a lot more flexibility for installation and can be maneuvered into place.”
Gavin Holland, Mining Hose Specialist
Do this instead:
Like the last issue, to avoid this problem you need to introduce flexibility to your pump piping. The two most common ways to do this are:
- Use a mining hose expansion joint with polyurethane lined pipe
This setup will allow for that slight alignment difference and ensure there are no weak points for the slurry to leak from.
- Use a one-piece mining hose reducer
Mining hose reducers have faster installation than expansion joints and are flexible. They work great for severe wear slurry as they have the best impact and vibration absorption.
One of our gold mining customers in the Northern Territory had this problem in their process plant.
Their rubber-lined pipe and flexible coupling set-up didn’t last to their scheduled shutdowns. Slurry would wear the flanges and the coupling joint.
They swapped to a mining hose reducer and their hoses now last twice as long as rubber-lined steel.
Improving reliability in your pump piping doesn’t have to be complicated
If you follow these simple steps, you won’t have to worry about your pump piping reliability again.
If you run into tricky piping or need specific advice, reach out and we will be able to help.
Many of our customers have made these changes and have seen big improvements in their uptime. Talk to us if you’d like to try some of these ideas in your plant.
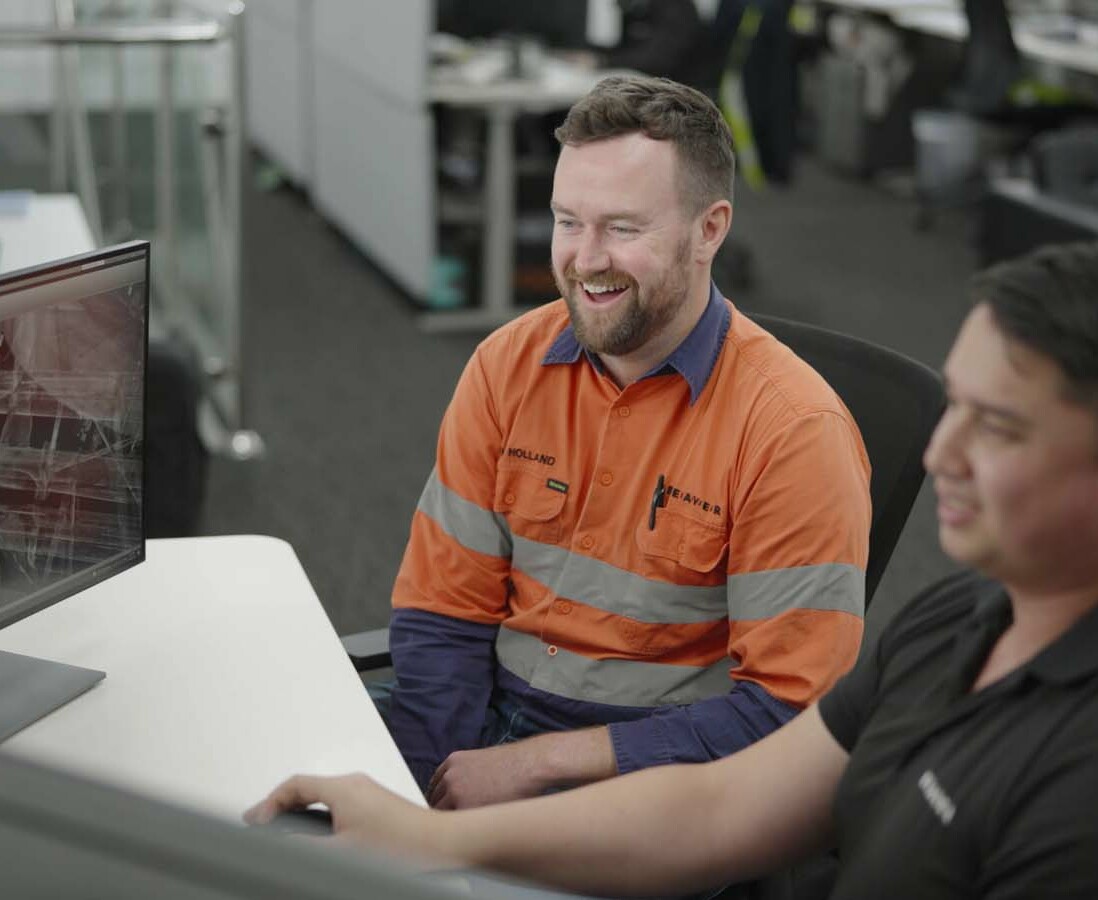
Get practical recommendations for your pump piping
Get in touch to setup a call with our piping specialists. We'll give you clear recommendations and advice to help you improve the wear life and reliability of your pump piping.
"*" indicates required fields