Design engineers are being pushed to do more with less.
Designing smaller plants on tighter budgets with faster design turnaround and shorter commissioning timelines.
All the while walking the schedule and budget tightrope.
So how can you deliver a new plant on time, on budget and running at optimal performance from day one?
Flexible piping.
Here’s 4 reasons why flexible piping should be part of your design toolkit.
1. Smaller Plants = Tighter Bends
Construction materials, supply chain and labour costs are at record highs. Mining companies are reducing the footprint of new process plants. In recent years, we estimate plant size has reduced by up to 20%.
Slurry piping systems must adapt too. Smaller plants mean tighter bends, less headroom and racking, and shorter piping lengths.
It is a challenge to specify piping that can fit into smaller spaces without kinking or blocking.
That is why flexibility is key. You need piping that can bend around tighter corners and negotiate space limitations.
The less time you spend struggling with spatial constraints, the more you can focus on optimising other aspects of plant design.
2. Stress-free Piping Connection
Commissioning a new plant comes with its fair share of challenges.
Poorly fitting piping should not be one of them.
As plant construction becomes more modularised, there’s a high risk of everything not fitting together.
Precise alignment is critical with rigid piping. Any error can lead to time-consuming and costly onsite reworking or lengthy refabrication lead times.
Flexible piping, with its ability for axial, lateral, and angular deflection, fits more easily into place.
This is particularly valuable during the installation, where delays mean lost revenue – for you and your client.
Here’s how the team at FMG Iron Bridge overcame fitment challenges by using super flexible mining hose.
3. Unravelling Spaghetti Junction
Spaghetti junctions are a constant frustration for design engineers – a complex network of branches running in all directions.
It’s a nightmare to install or replace rigid spools in this area. Tightly packed spaces and no room for error means there’s a high potential for poor fitment.
That can play havoc on your commissioning deadline.
Flexible piping simplifies this. It’s easier to route the pipes in ways that reduces clashes with other branches or permanent instrumentation.
This makes future maintenance and potential upgrades much less of a challenge.
4. Cut Commissioning Time – and Costs
Time is money – especially during commissioning.
Flexible piping reduces the installation time.
How? By reducing the number of spools.
For example, three spools – a straight, an elbow and another straight – is replaced with one hose. That’s fewer end connections, bolts and supports needed.
It will also shorten procurement windows. With faster commissioning and easier installation, the plant is up and running quicker.
Consider how this could increase your project efficiency and deliver a more streamlined and efficient process from conception to completion.
Flexibility Matters in Modern Plant Design
Tight schedules, limited budgets, and complex spatial requirements are no longer the exception in plant design.
That’s why top design engineers are looking at new ways to improve plant optimisation without compromising on productivity.
Flexible piping is one way they are achieving this. Less time spent during design and installation is helping them deliver on-time, on-budget, and fit-for-purpose process plants that meet their client’s design and operational goals.
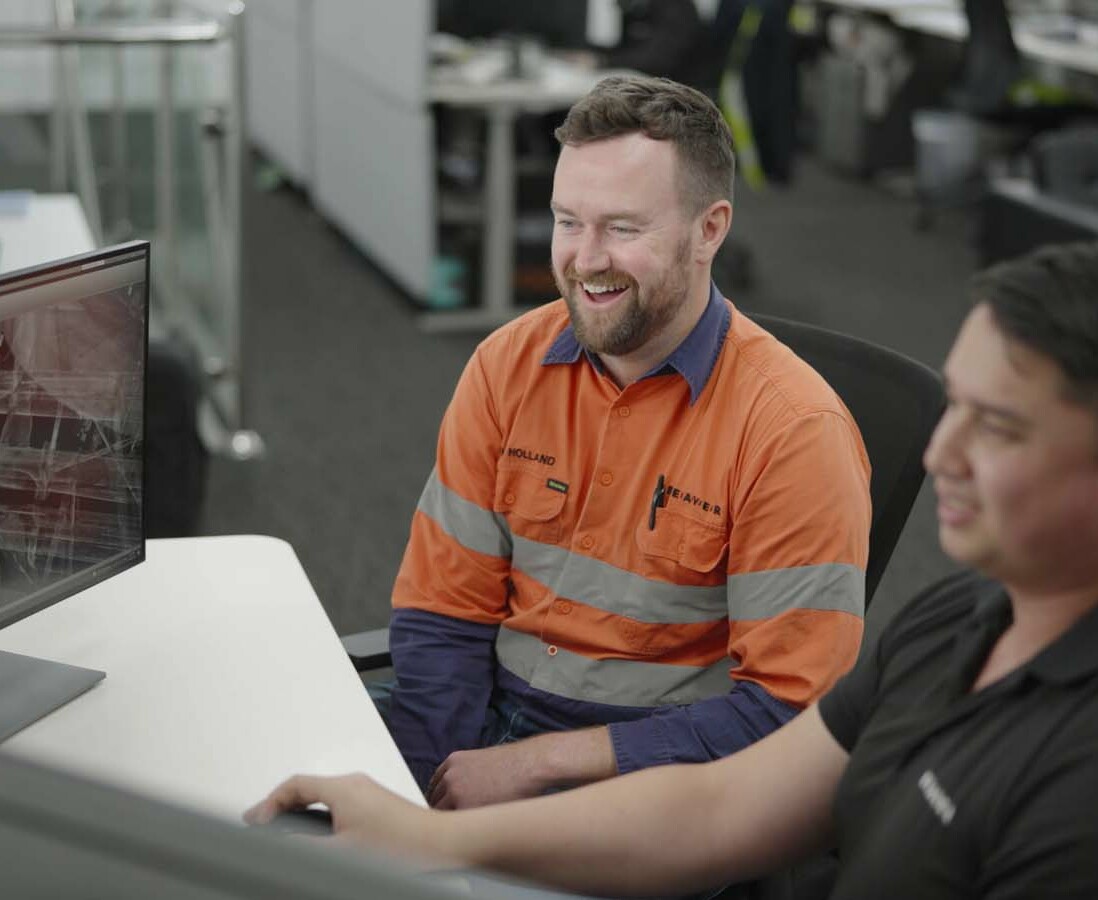
Let's talk about flexible mining hose for your project
We'll share practical examples of projects like yours being completed on time and on budget using flexible mining hose, and how you can do the same.
"*" indicates required fields