How often have you received a lined pipe elbow on site, only to find that it doesn’t fit? We know this happens often—and it’s frustrating. Lined pipe can be unforgiving. Which is why some of the world’s leading mine sites are starting to use mining hose on bends.
Not only is mining hose easier to install, but it can make a big difference to the wear performance and lifespan of your plant’s slurry piping system. Here, we explain three advantages to using mining hose on bends.
1. Geometry and fit
There are many technical considerations if you’re using hard piping on a bend in your plant. The bend radius, tangent lengths, and end connection angles all must be spot-on, so when the spool arrives on site, it fits perfectly. There’s a lot to get right and the potential for mistakes is high.
Mining hose fits better on bends because it has:
Greater axial deflection
You can stretch or compress the hose between two fixed points.
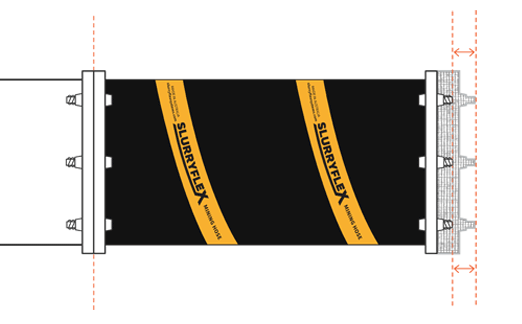
Axial deflection
Greater lateral deflection
You can curve the hose where there’s an offset or misalignment between the two pipes you’re trying to connect.
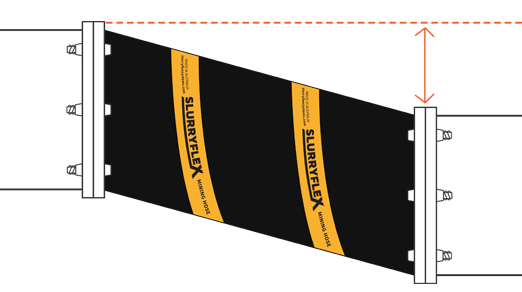
Lateral deflection
Greater angular deflection
You can flex the hose if the angles of the end connections or coupling are misaligned.
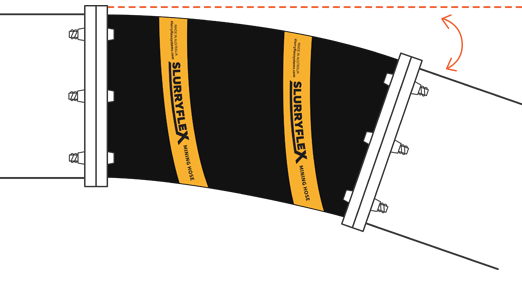
Angular deflection
Greater torsional deflection
The hose can twist when it needs to during installation and service.
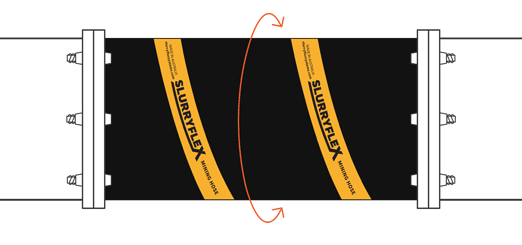
Tortional deflection
If a bend is going to face any of the forces listed above, a hose bend is going to be a better option than a rigid spool.
A hose’s flexibility provides radically greater tolerance when you’re trying to connect or align with existing pipework. And that extra wriggle room makes it easier during installation.
Plus, mining hose will also better absorb vibration both from your pumps and from fast-moving slurry travelling through the line.
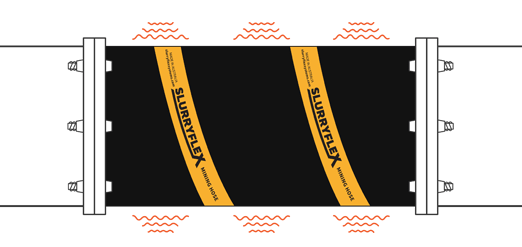
Vibration absorption
Which leads us to the second advantage of using mining hose on bends.
2. Absorption and deflection of particle impact
Mining hose elbows provide more ‘give’ than rigid pipe. This means when hard and fast slurry hits the pipe wall, particles are deflected rather than absorbed. So you end up with substantially increased wear performance compared to a rigid lined-pipe bend.
To understand this, let’s touch on elastic and plastic deformation and its role in pipe wear.
Elastic deformation
Elastic deformation can be thought of like a ball bouncing on a trampoline. When a particle hits the pipe liner, it causes a small deformation in the lining, which returns to its normal state once the particle has rebounded.
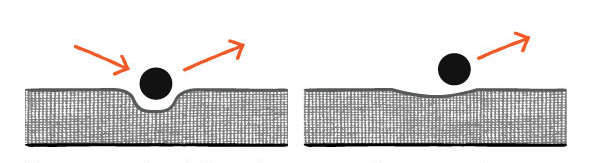
Elastic impact: Temporary micro deformation leads to lower wear rate
Plastic deformation
Plastic deformation is more like a stone hitting your car windscreen. It creates a permanent deformation. Rather than bouncing off, when a particle impacts the liner, it causes a tear or fracture.
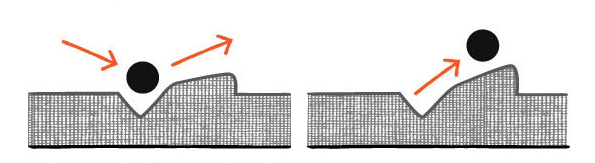
Plastic impact: Cut, tear, or fracture leads to higher wear rate
Both wear mechanisms occur in slurry piping, but plastic deformation will result in higher wear on pipes.
With rigid pipe, the liner—such as rubber or polyurethane—provides a level of elastic deformation.
However, with mining hose, the inner liner provides wear deflection, plus the entire carcass of the hose will absorb vibration and spread the impact from large particles or high-velocity slurry. So, you get an extra layer of particle energy absorption and dispersion that doesn’t happen with hard piping.
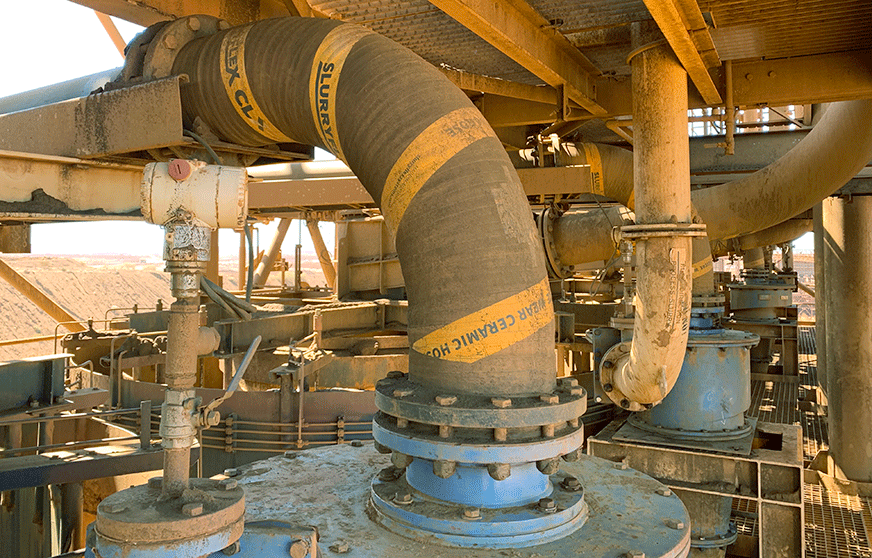
Ceramic-lined mining hose is a good option for tight radius bends
In small radius bends, like cyclone overflows, we often see accelerated wear which leads to ongoing maintenance issues.
When this happens, it’s worth looking at ceramic-lined hose because it does two things to reduce wear in this situation. The ceramic tiles increase the wear life of the pipework by deflecting the particles. And, the rubber hose absorbs and dissipates impact from the high-velocity slurry.
3. Easy bore matching for better flow and wear
This photo from a gold plant shows leading edge wear because the pipes were not bore matched. It caused recurring leaks and downtime until the pipes were replaced.
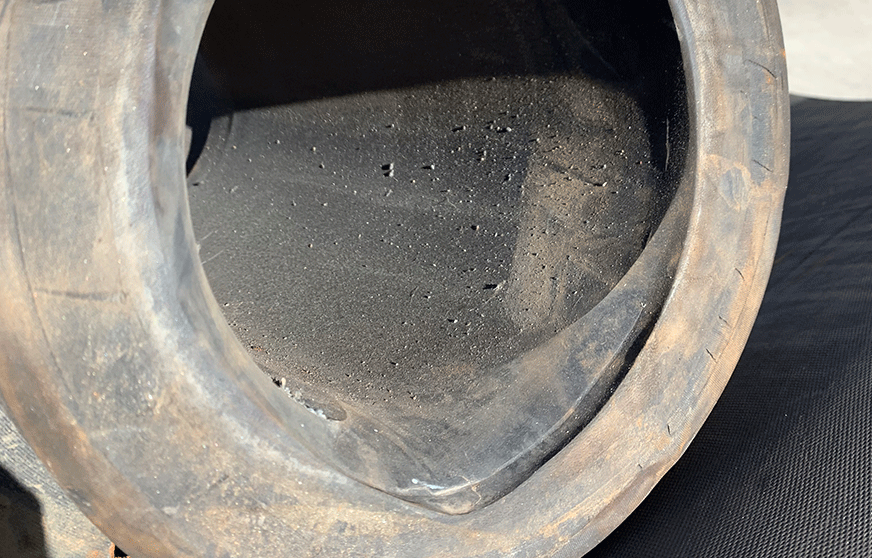
Leading edge wear happens when IDs are not bore matched
Matching the internal diameter (ID) of the slurry hose to a set size reduces leading edge wear on the flange faces and the hose liner. This is easier to do on mining hose because of the way its manufactured.
Mining hose bends are built on mandrels from the inside out, so it allows you to increase the liner thickness. Your mining hose supplier will either have a mandrel built to that size, or you can specify this when ordering your elbow or bend.
Plus, you can build the outer arc of the bend (where there’s likely to be more wear) with a thicker liner without compromising the hose ID.
Reliability is a team effort
When debottlenecking or upgrading parts of your plant, it’s worth looking at whether some of the rigid elbows in your piping system would work better as mining hose bends.
In our experience, the best slurry piping systems have a combination of hard lined-pipe and flexible mining hose. This gives you the best of both worlds—the strength of steel with the flexibility and increased tolerance of mining hose.
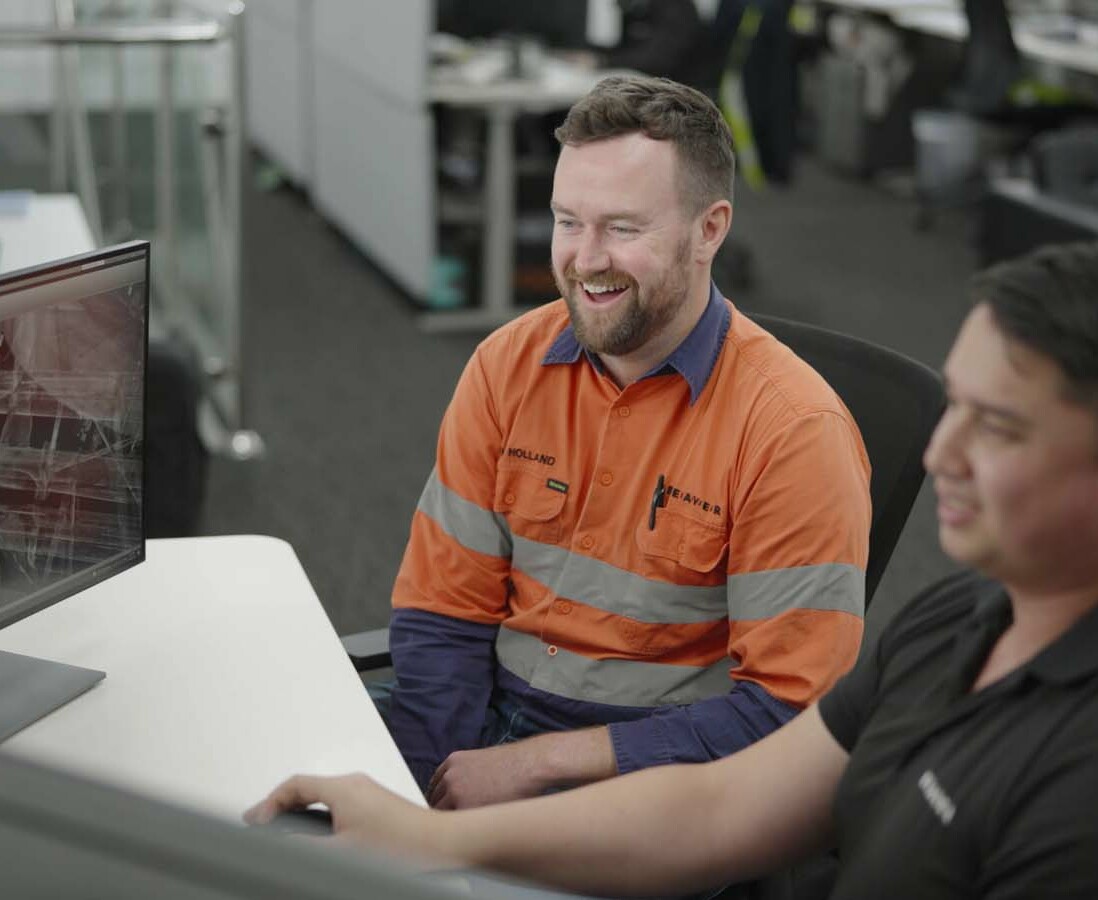
Tired of replacing the same piping elbows?
Find easy wins for your plant. We’ll share real examples of sites like yours getting longer wear life and better reliability from their piping elbows and how you can achieve the same.
"*" indicates required fields