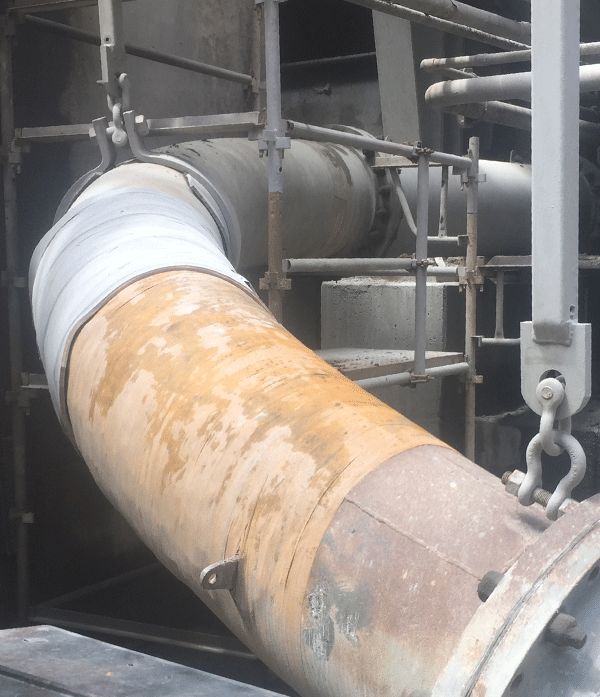
The problem
The customer had been running seawater through cement-lined steel pipe to cool the autoclave section of the process plant.
But the cement lining was deteriorating fast from the seawater, leaking through and corroding the pipe—causing headaches for the maintenance team.
In our experience, cement-lined steel is fine for short periods of time but it can’t withstand long exposure to seawater. So, we helped AECOM review all the options and select a liner that could handle a wide temperature range while providing high hydrolysis resistance.
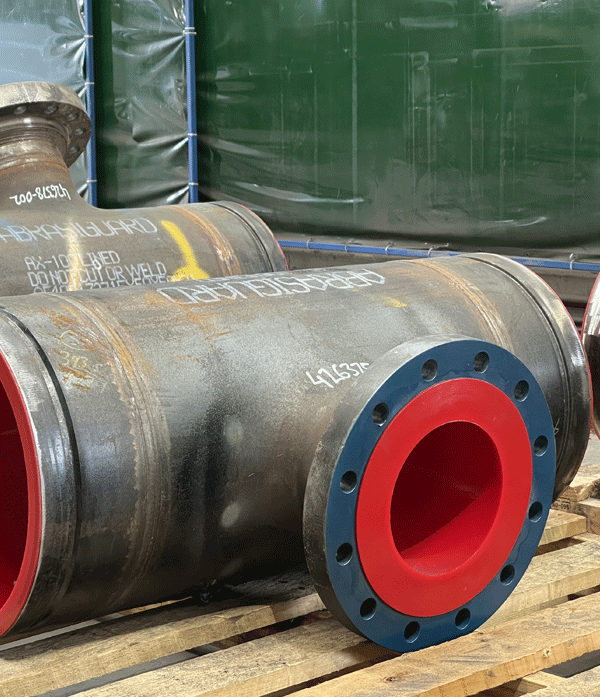
Choosing the right liner
We had considered ceramic lining, but typically this exposes its adhesive grout between the ceramic tiles or sleeves to the fluid. This can provide a leak path to the underlying vulnerable metallic substrate. Ceramics are also typically expensive and very labour-intensive to install and maintain.
HDPE piping is unsuitable in high-temp applications because it loses its strength and pressure rating quickly as temperature increases.
Abrasiguard polymer-lined pipe provides a single continuous liner system cast in situ inside the pipe with no potential leak path. That means it’s a good choice for applications where there’s long-term immersion in high-temperature seawater (without hydrolysis or other degradation).
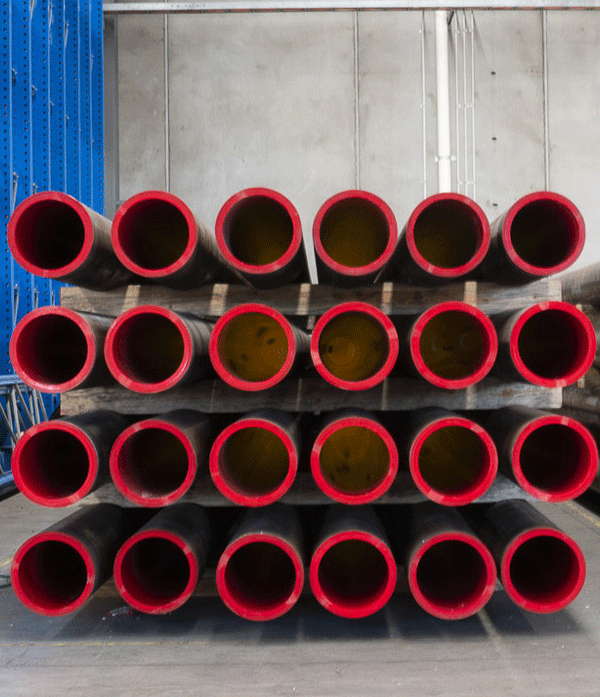
Less maintenance, less hassle
The design engineers decided that Abrasiguard polymer-lined pipe would be the best option because it provides a longer wear life when transporting seawater. In fact, we expect it to last for 20 years, based on similar applications. They also mentioned that the liner smoothness has taken pressure off the pumps, so over time they will experience less wear as well.
It’s a great result for AECOM and the customer. Now, they can focus their efforts on improving throughput in other areas of the plant.