Aeris Cracow Gold Mine – Slurryflex CLX for Ball Mill Piping
Would you rather replace ball mill piping every a) 10 weeks or b) 10+ months?
In 2022, the maintenance team leader at Aeris Cracow gold mine gave us a call about fast wearing piping from the ball mill discharge pumps.
His team was only getting 10 weeks out of HDPE bends in this part of the plant. It was frustrating, time-consuming, and impacting throughput.
We knew we could help him because we see this problem all the time.
Accelerated wear on bends is typically caused by two issues:
- Slurry hitting the walls of the piping when it changes direction. You end up wearing one spot (generally the outer arc of the bend). It’s common in rigid bends as there’s no flexibility in the line to handle particle impact
- Wrong piping type. HDPE is good for process water and other low wear applications but will wear quickly under abrasive conditions
Ceramic-lined mining hose is a good option for ball mill piping. Mining hose can better absorb and deflect high velocity slurry. The ceramic tiles embedded into the hose liner increase the wear life but still allow for flexibility and movement. Plus it’s easier to install than rigid piping.
The maintenance leader decided to trial Slurryflex CLX mining hose to see if it would last longer than the current piping. We also recommended he standardise the bends to one size and angle. It reduces the costs in holding replacements as one piece can be used in more than one place.
Our Brisbane team built and sent the Slurryflex CLX DN150 bends to site.
10 months on and they’re still going strong.
Stop making work for yourself and your team and get off the pipe replacement merry-go-round.
Client
Application Ball mill piping
Location QLD
Commodity Gold
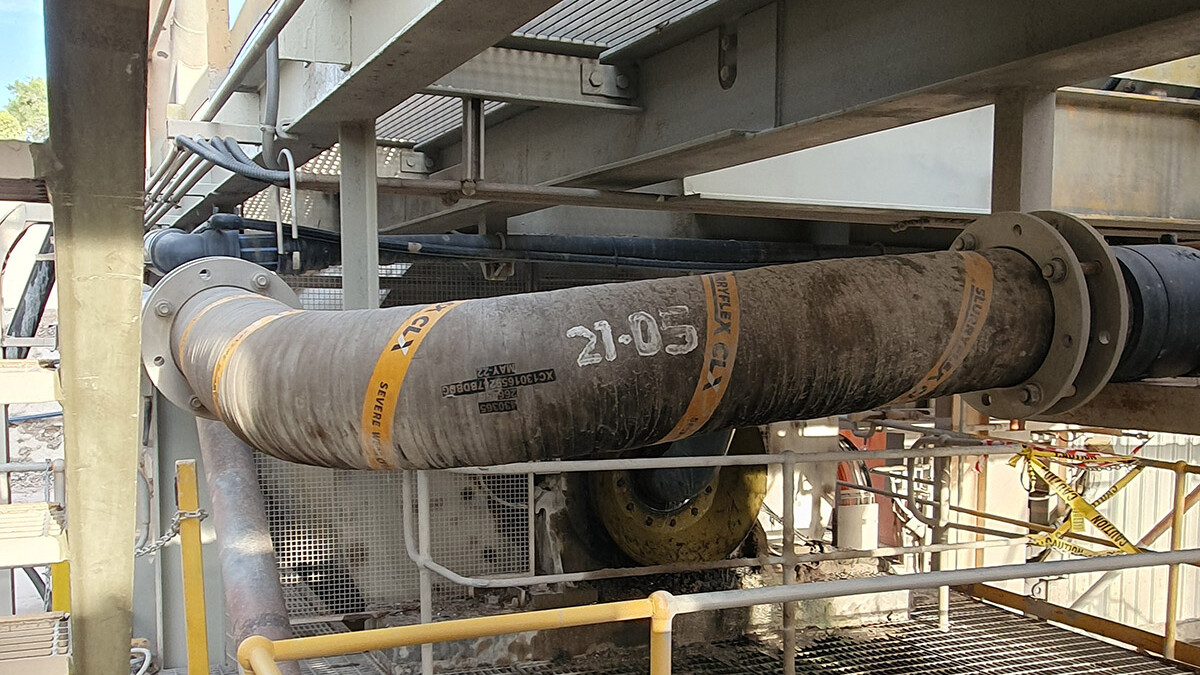

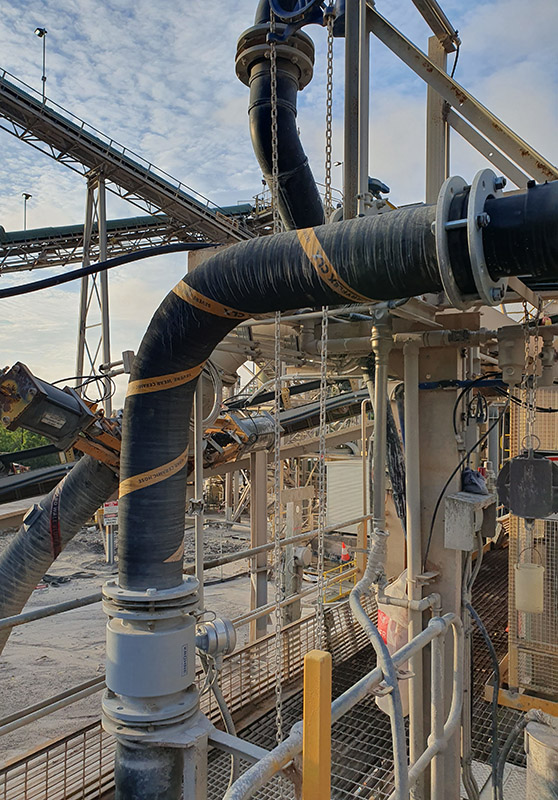
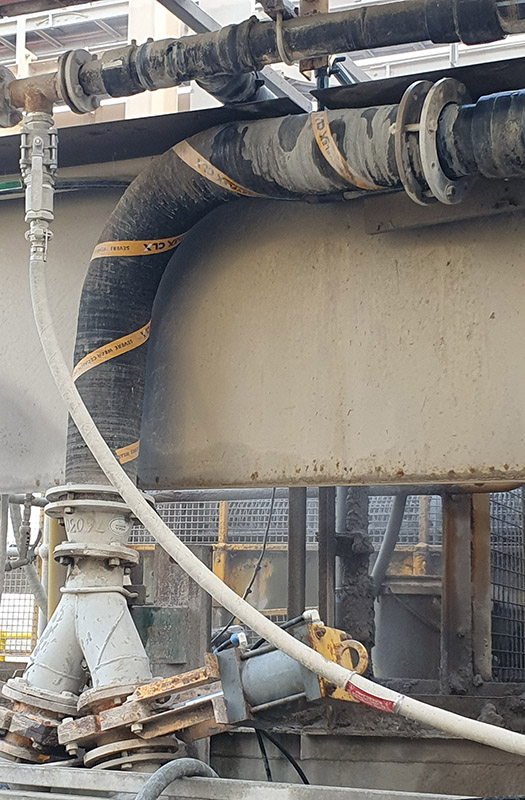
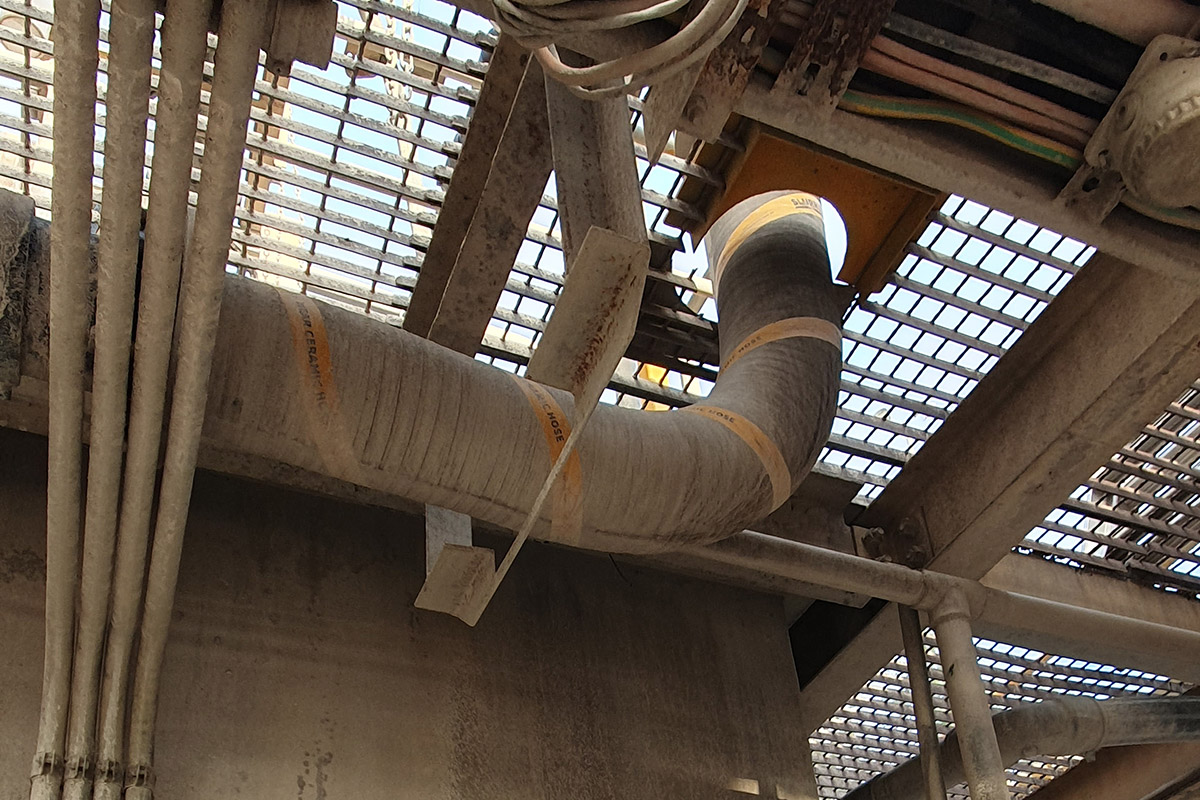
Related projects
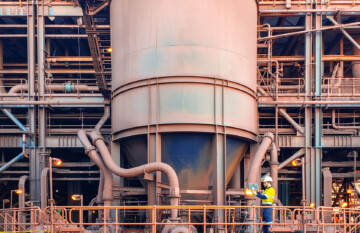
How Roy Hill Solved Costly Unplanned Piping Maintenance for Good
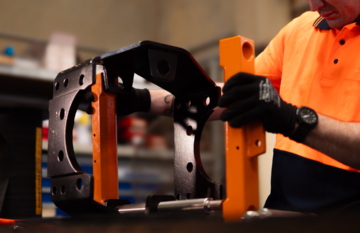
WA Lithium Mine get 12x Longer Wear Life in Slurry Control Valves
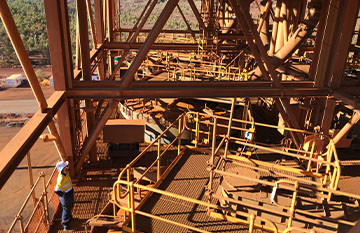
8x Longer Lifespan for Cyclone Overflow Piping at FMG Solomon Mine
We're here to help
Got questions? Need advice? Tap into our experience and get specialist advice from our friendly team.
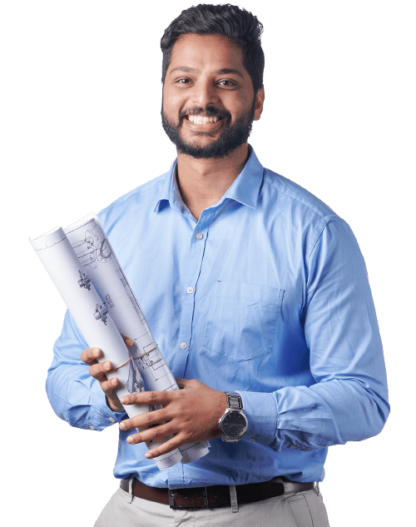

Slurry piping audits
Solve slurry piping maintenance problems for good. No more leaking pipes, no more unplanned shutdowns.